RFID Based Emergency Evacuation System
A Complete Employee Safety Tool using IoT
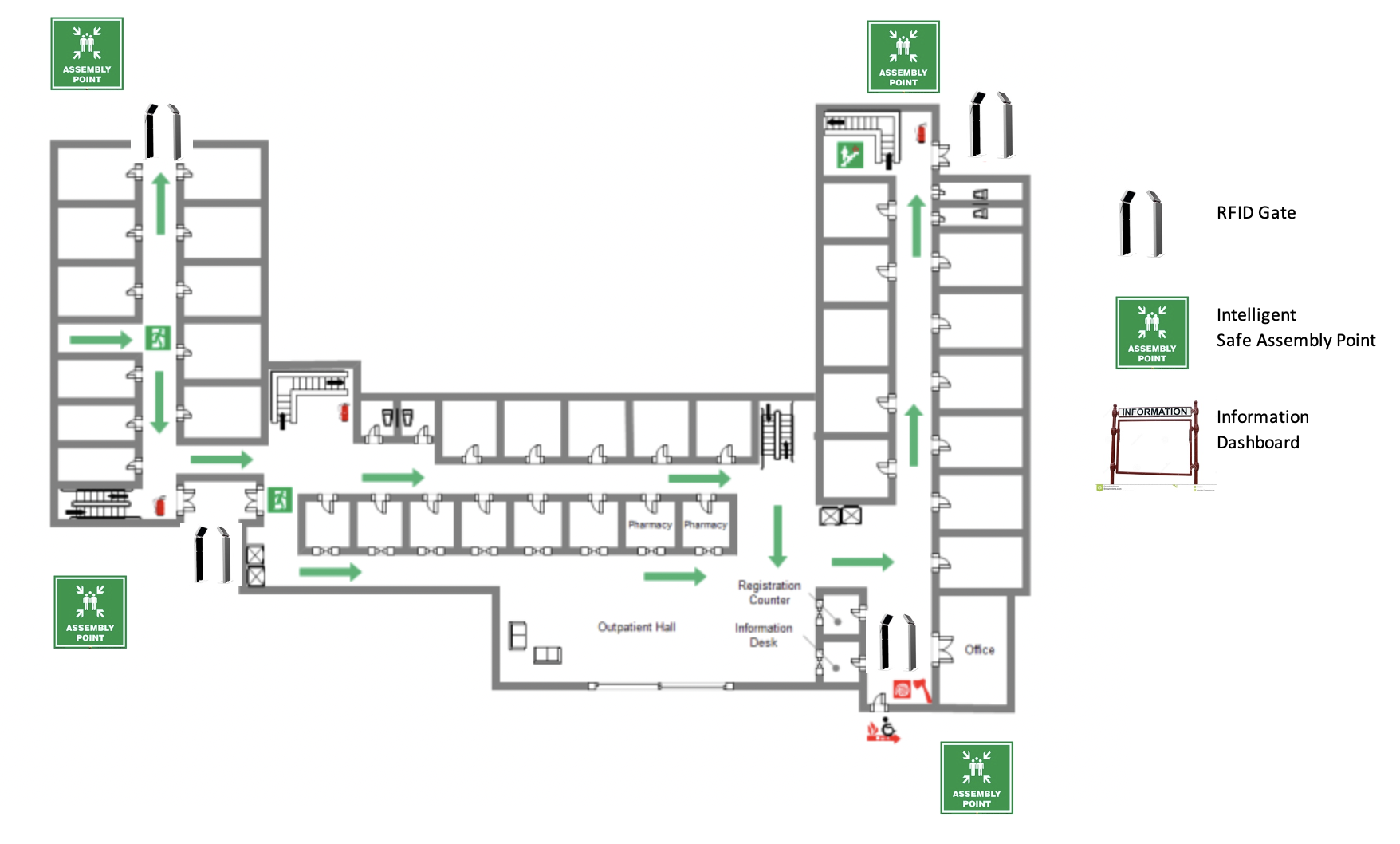
Product Feature
Every facility should have a well-documented process in place to keep its employees safe. RFID technology advancements are providing businesses with scalable safety measures that are used to aid in emergencies, evacuation, and mustering.
Emergency Situations
Natural disasters such as tornadoes, flash floods, and wildfires can pose a significant threat to your facility, depending on your location. Weather disasters can strike quickly, necessitating an evacuation or shelter-in-place plan. Another scenario involves man-made disasters, such as a building fire or toxic release, which necessitates an immediate evacuation.
According to the Occupational Safety and Health Administration (OSHA), every company should have one emergency warden for every 20 employees. These wardens are in charge of sweeping a building during an evacuation and are the last people to leave in the event of an emergency. This person is also in charge of ensuring that employees gather at the mustering (or safe zone) area. RFID employee tracking system using UHF RFID badge helps organizations to track their employees during emergency situations.
RFID UHF to the rescue
Even with a designated warden, an evacuation can present a number of challenges where RFID technology can fill the gaps. When an emergency occurs, an employee may be out of the office or in another part of the building, and there may be a number of visitors and contractors in your facility.
It’s interesting to note that, despite the fact that RFID was invented during WWII to identify enemy planes, new applications for it are still being discovered. Hexahash provides innovative solution offerings using an RFID employee tracking system to transform emergency mustering in industries.
RFID makes it ideal for evacuation. How? It can precisely identify up to 1200 and above tagged people or items at the same time – all in one second. There is no need for RFID readers and tags to make visual contact. They do not need to be presented to the reader. Instead, they can be concealed beneath working clothes, in a pocket, or in a bag. Tags come in a variety of sizes and shapes. RFID labels and tags or RFID badges worn by employees easily detected by RFID antenna which connected to the RFID reader transmit data to the centralised cloud server or on-premise server.
Why is UHF RFID technology ideal for employee safety during an emergency evacuation?
- Get to know the exact headcount inside the premises and in the safe assembly area
- Employees do not need to do anything to be identified – simply wearing a tag-lanyard suffices.
- There is no visual contact between the tag-lanyard and the RFID UHF reader.
- For precise identification, a comfortable and light tag lanyard can be used.
- Individual RFID systems that address all of a company’s specific needs can be easily designed.
- Walk-through Gates in each entry and exit points keep track of employee in-and-out movements precisely and passively
UHF passive RFID solution is logically a right-fit approach to all evacuation challenges. It proposes solutions to the current shortcomings in evacuation coordination. It is an intriguing and valuable alternative to the most commonly used methods. Furthermore, it is perfectly aligned with legal regulations. Employers are increasingly being asked to use technological solutions that allow for precise and instant identification. RFID UHF is ideal for such applications.
Components
Smart Assembly Point Sign-Board with Built-in BLE and RFID Reader
BLE Enabled Walk-Through RFID Gate
Employee Badge with UHF RFID and BLE Beacon
RFID Antenna with Built-in BLE Gateway or RFID Antenna only
USB UHF RFID Desktop Reader for Mapping
LED TVs Displaying Head Count of Employees "in and out" of the premises
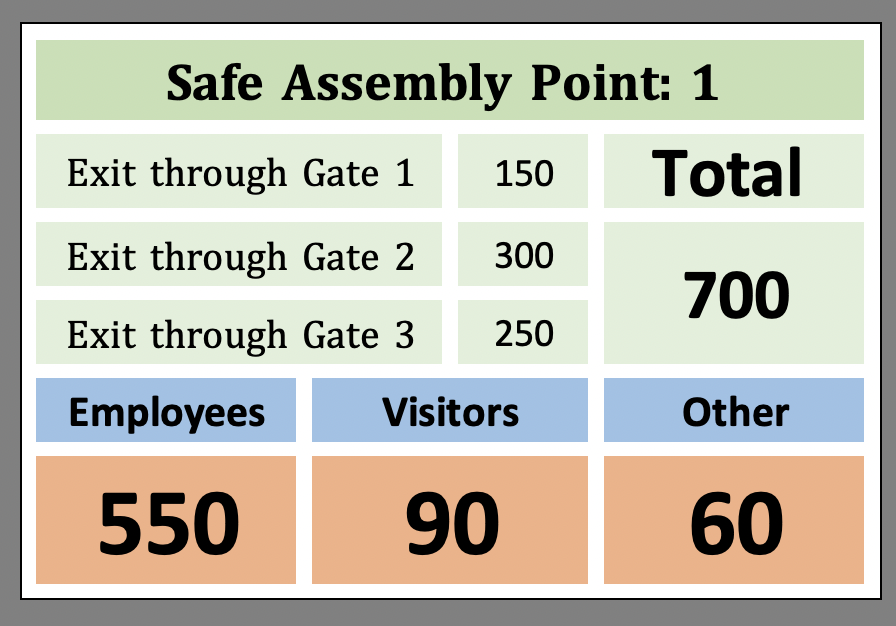
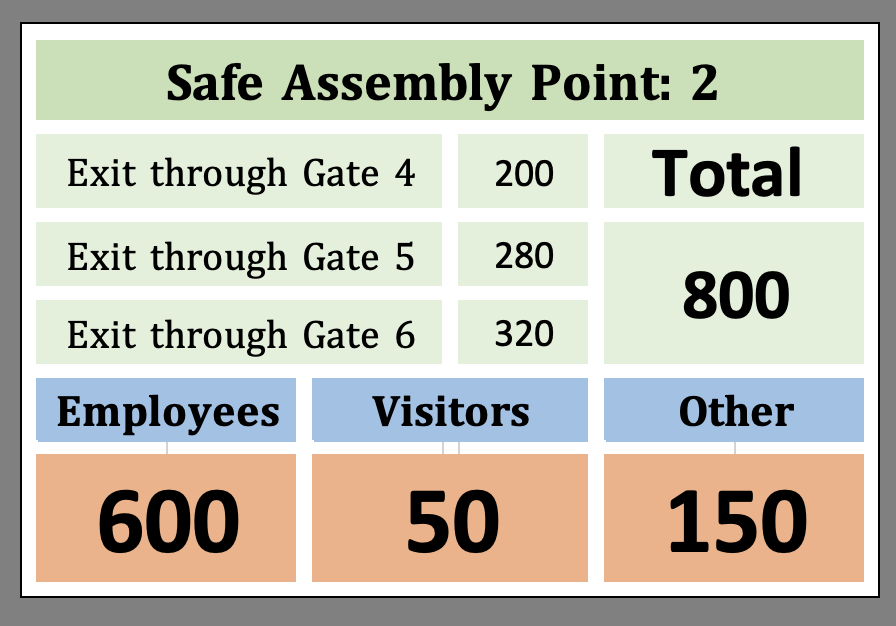
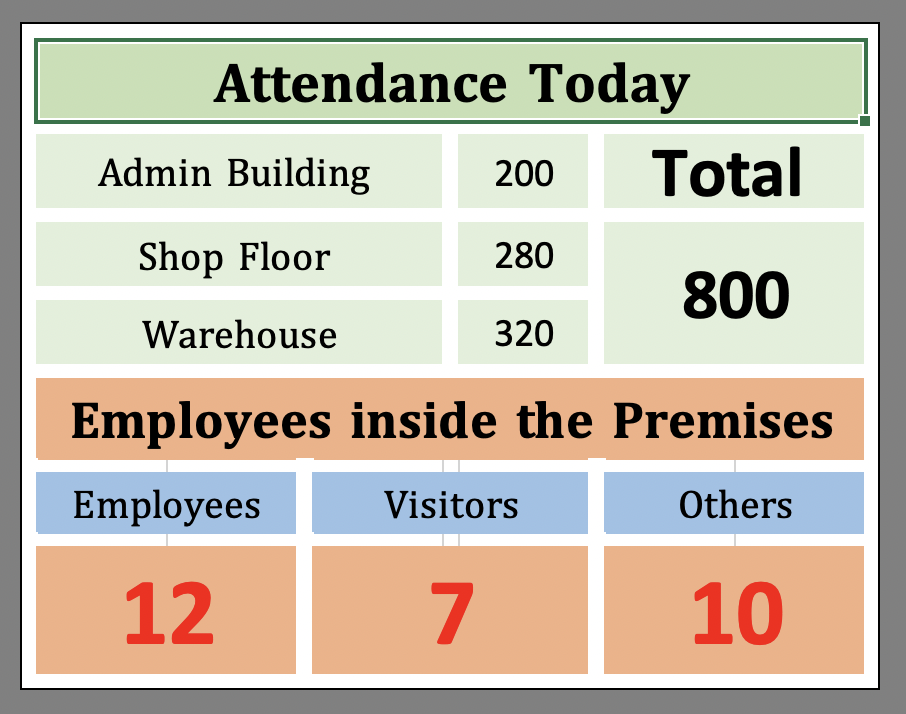
Final Result
The list of people at the emergency assembly point is compared to the list of people from the evacuated area using RFID. As a result, the coordinator is aware that no one was left behind. Fatal consequences are avoided.